Cement Leaves More Than a Gray Mark
While cement is responsible for infrastructures all around the world, it is also responsible for a considerable carbon footprint.
Reading Time: 3 minutes
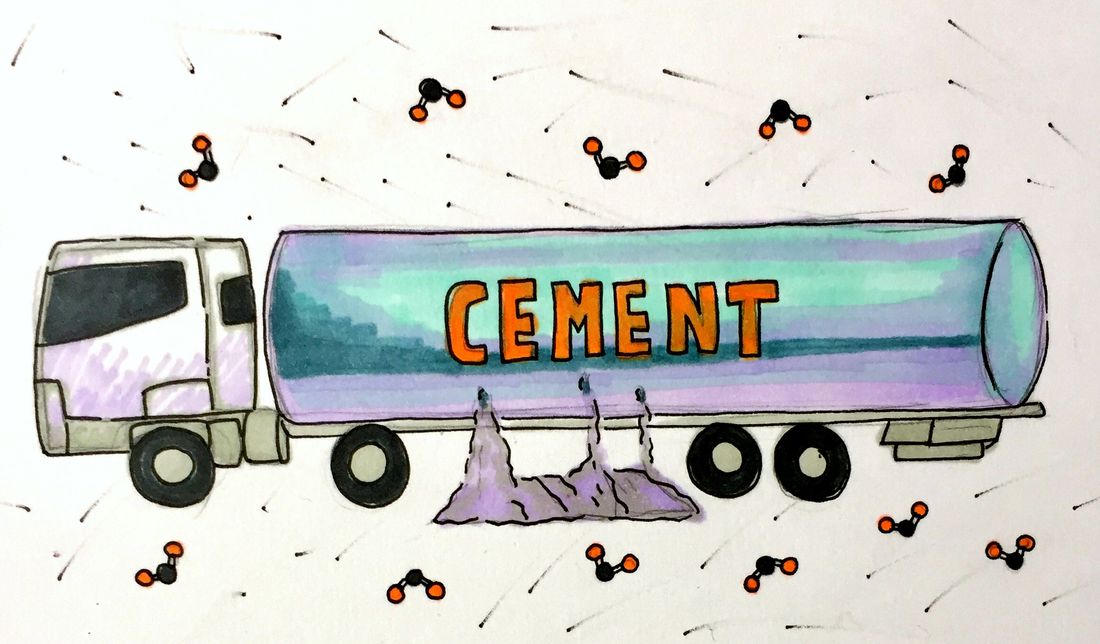
Cement is the most commonly used man-made material. From forming sidewalks and roads to impressive buildings, this material is an essential component of modern construction. In fact, the Sydney Opera House, the Lotus Temple in Delhi, and the grandiose Pantheon in Rome were all architectural feats made possible by cement. However, cement has left much more than a gray mark on infrastructures around the world; it has left a significant carbon footprint as well.
According to Chatham House, over four billion metric tons of cement are produced globally every year, amounting to approximately eight percent of annual global CO2 emissions. This makes the cement industry the second-largest carbon emitter, after the steel and iron industry. Some estimates even predict that as the global population grows and demands increase, cement production may rise by 23 percent by 2050. The Paris Agreement, a global treaty of 197 members ratified in 2016, lays down the groundwork to combat climate change. The treaty aims to lower global greenhouse gas emissions back to healthy levels by limiting global warming to two degrees Celsius, at most. To reach the temperature goal set by the Paris Agreement, by 2030, the cement industry will need to reduce its yearly carbon emissions by 16 percent. Consequently, cement production has become an increasing concern for scientists and cement producers alike, since the current state of the cement industry is bound to jeopardize the Paris Agreement’s targets for climate change.
The first step in reducing emissions in the cement industry is understanding how manufacturing cement creates emissions. The manufacturing process begins by grinding and crushing raw materials such as limestone and clay. The crushed materials are then blended with ash or iron ore and mixed in a kiln at extremely high temperatures. The resulting ingredients undergo calcination, a process that extracts calcium oxide and carbon dioxide and produces a clinker, a sphere-like solid. When the clinker is cooled, it is ground and mixed with materials like gypsum and limestone to produce cement. The calcination step accounts for a shocking 90 percent of emissions, while transporting, grinding, and cooling are responsible for less than 10 percent. Therefore, many researchers are looking for ways to reduce the emissions from clinker production or even from the entire manufacturing process itself.
To do so, a research team from the University of California, Los Angeles, is developing a product called “CO2NCRETE” to combat carbon emissions from the cement manufacturing process. CO2NCRETE uses a process known as “carbon upcycling” to convert CO2 from industrial activities in factories and power plants into carbon-neutral cement. There is no processing required, meaning the CO2 conversion to this product can occur right at the site of industrial activities. As a result, this more eco-friendly cement could potentially replace Portland cement, the traditional cement used to create concrete. Not only that, CO2NCRETE may directly reduce carbon emissions produced in power plants and factories through carbon upcycling.
Other researchers are trying to take advantage of the fact that concrete, a building material with cement as a component, has the ability to soak up carbon dioxide. Though the absorption of carbon dioxide is slow, occurring over decades, it is possible that a significant amount of carbon emissions released during calcination can be absorbed. A Nature Geoscience paper in 2016 revealed that concrete has absorbed 43 percent of the original emissions released during the creation of cement globally. Researchers are developing methods to improve and speed up this process of absorption. In the future, concrete could reverse carbon emissions during the creation of cement.
While many innovative solutions are arising to combat carbon emissions in the cement industry, there are still challenges. The carbon industry lacks the incentive to change and adopt these new technologies. Traditional Portland cement is a reliable and safe building material, while many of the newer substances are less thoroughly researched. Because of this, the introduction of newer materials for the construction of important infrastructures is subject to much concern about safety and reliability. Additionally, using these new materials requires approval from regulatory groups, which is difficult to get. With the growing global population, demands for affordable homes are increasing, which will increase the consumption of cement and result in more carbon emissions.
However, all is not lost. Despite the cement sector’s reluctance to change, the rising concern for climate change has helped raise acceptance of cement alternatives. CEMEX is a leading figure in carbon reduction in the cement industry and has supported the development of climate-friendly infrastructure around the world. LinkedIn is another company that is developing a carbon-neutral technology to reduce emissions from cement. One can be a part of this movement by raising awareness about climate change and its effect on the world. Fundraising for and supporting CEMEX, LinkedIn, or other large organizations fighting against climate change can change the world for the better.